Тема Поверхностное пПластическое деформирование как метод упрочнения поверхностей деталей
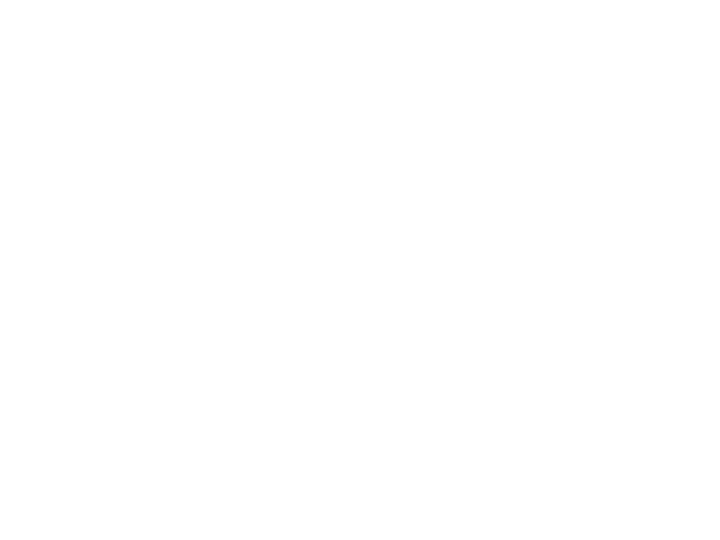
- Рубрика: Презентации / Другие презентации
- Просмотров: 180
Презентация "Тема Поверхностное пПластическое деформирование как метод упрочнения поверхностей деталей" онлайн бесплатно на сайте электронных школьных учебников edulib.ru
Поверхностное пластическое деформирование (ППД) - это вид упрочняющей обработки, при котором не образуется стружка, а происходит пластическое деформирование тонкого поверхностного слоя заготовки.
Сущность способа заключается в следующем.
Под давлением деформирующего инструмента микровыступы (микронеровности) поверхности детали пластически деформируются (сминаются), заполняя микровпадины обрабатываемой поверхности, что способствует повышению твердости поверхностного слоя.
Упрочняющую обработку поверхностным пластическим деформированием применяют на финишных операциях технологического процесса, вместо или после термообработки, и часто вместо абразивной или отделочной обработки.
ВИДЫ ОБРАБОТКИ
1 Обкатывание и раскатывание
2 Калибрование
3 Дробеструйная обработка
4.Алмазное выглаживание
ОБКАТЫВАНИЕ И РАСКАТЫВАНИЕ
В соответствии с ГОСТ 18296–72 поверхностное пластическое деформирование при качении инструмента по поверхности деформируемого материала называется накатыванием.
В свою очередь накатывание подразделяется на обкатывание и раскатывание , в зависимости от того какие поверхности обрабатываются: выпуклые (валы, галтели), плоские или вогнутые (например, отверстия).
По своему назначению накатывание подразделяется на сглаживающее, упрочняющее, рельефообразующее.
А – упрочняющее раскатывание б- упрочняющее обкатывание
Р - усилие давления, n- частота вращения, S- подача
Сущность процесса заключается в силовом воздействии на поверхность заготовки инструмента высокой твердости. В качестве такого инструмента применяются твердосплавные или закаленные ролики. Давление осуществляется только в зоне контакта инструмента и заготовки.
Для накатывания применяют стандартные шарики или ролики различной конструкции и профиля.
Материал - инструментальные стали ХВ4, ХВГ, Х12М, Р6М5
Обкатыванием и раскатыванием отделывают и упрочняют цилиндрические, конические, плоские, фасонные наружные и внутренние поверхности.
Инструмент и оборудование для обкатывания и раскатывания
Обработка обкатыванием и раскатыванием проводится на токарно-винторезном станке.
Инструмент устанавливается в резцедержателе. Деталь устанавливается в патроне или в центрах.
КАЛИБРОВАНИЕ ОТВЕРСТИЙ
Калибрование (деформирующее протягивание, дорнование) – чистовая операция обработки отверстий деталей машин пластическим деформированием
Эту операцию выполняют перемещением с натягом деформирующего инструмента (оправки с деформирующими элементами, или шариками) на протяжных станках и прессах с использованием смазки.
Поверхностное дорнование обеспечивает обработку отверстий с точностью 6-9 квалитет и шероховатость Ra=0,32-0,05мкм
Калибрование (дорнование) отверстий:
а — шариком; б — оправкой; в — протягиванием пуансона;
г — изменение диаметра отверстия после калибрования d-d1
1 — деталь 2 — шарик 3 — оправка 4 — пуансон
Калибрование отверстий требует достаточно точной и чистой предварительной обработки. Точность отверстия после дорнования повышается на 30%.
Процесс обработки калибрующим инструментом проводиться при обильной смазке. В качестве смазывающих жидкостей рекомендуется при обработке стали машинное масло, сульфофрезол, а при обработке чугуна — керосин и мыльная вода.
Короткие отверстия калибруются на прессах путем проталкивания оправки (пуансона) или шарика,
а отверстия с отношением длины к диаметру ℓ > 8d протягиваются калибрующим пуансоном на протяжных станках.
ДРОБЕСТРУЙНАЯ ОБРАБОТКА
Обработка дробью (ОД) осуществляется ударами чугунной или стальной дроби по деформируемому материалу с целью упрочнения поверхности детали.
К основным технологическим параметрам при выборе режимов обработки дробью относятся:
диаметр дроби,
скорость полёта дроби,
время обработки,
угол атаки.
От этих параметров зависят степень пластической деформации поверхности, глубина упрочненного слоя, величина остаточных напряжений и шероховатости поверхности.
Выбор дроби определяется материалом, размерами и конфигурацией детали. Применяется:
литая стальная или чугунная дробь (диаметром 0,2…3,6 мм),
шарики для подшипников (1…10 мм),
стальная колотая дробь (0,005…0,3 мм),
стеклянные шарики (0,25…1,2 мм)
.
Стеклянные шарики чугунная дробь стальная колотая дробь
Заготовку помещают в закрытую емкость. Дробь под воздействием потока воздуха или за счет центробежных сил во вращаюшейся емкости с большой скоростью ударяет о заготовки. Скорость вылета дроби 50-85м/с
Исходная щероховатость не меняется происходит только наклепывание- упрочнение поверхности.
Для дробеструйного наклепа обычно применяют механические и пневматические дробеметы.
Механический дробемет
1- элеватор
2-заготовка
3 –сепаратор
4 – склиз
5- приемная воронка центробежного аппарата
6-рабочая камера
Абразивный материал из рабочей камеры 6 поступает в элеватор 1, затем в сепаратор 3, в котором абразивные частицы отделяются от отходов, поступающих по патрубку в очистные устройства. Абразивный материал по склизу 4 попадает в приемную воронку центробежного аппарата 5 и направляется на обрабатываемую поверхность заготовки 2.
Метод дробеструйного упрочнения применяется для обработки лопаток турбин, рессор, пружин, зубчатых колес, спиральных сверл, матриц, пуансонов, обработки сварных швов
АЛМАЗНОЕ ВЫГЛАЖИВАНИЕ
Алмазное выглаживание представляет собой процесс пластического деформирования исходного микропрофиля под действием усилия, приложенного к алмазу (или другому сверхтвердому материалу).
Алмазное выглаживание используется с целью получения высокого качества поверхностного слоя деталей и повышения их эксплуатационных свойств.
Инструмент для выглаживания состоит из наконечника с алмазом и державки. Державка при работе на токарном станке крепится на суппорте или в пиноле задней бабки.
Нагружающие механизмы державок имеют упругие элементы (пружины), обеспечивающие непрерывный контакт алмаза с обрабатываемой поверхностью и примерно одинаковую силу выглаживания.
3- алмаз, 1- оправка, 2-державка Схема обработки
Эту операцию применяют для упрочнения изделий твердостью до 65 HRC, а также вместо операции окончательного шлифования, полирования, доводки и суперфиниширования поверхности.
Метод универсален и широко применяется для обработки стальных закаленных или термически неупрочненных деталей, с поверхностными покрытиями и без них, а также деталей из цветных металлов, их сплавов, высокопрочных чугунов.
Выглаживание выполняют специальными инструментами - выглаживателями, оснащенными сферическими или конусообразными деформирующими элементами, изготовленными из синтетических сверхтвердых материалов - карбонада, эльбора-Р, а так же из природных алмазов или твердых сплавов
. Достоинства алмазного выглаживания
микронеровности на поверхности могут быть уменьшены в несколько раз (до Ra 0,1…0,5),
микротвёрдость увеличивается на 5–60 % (при глубине наклепанного слоя до 400 мкм).
Недостатки
Учитывая повышенную хрупкость алмаза, не следует обрабатывать выглаживанием:
прерывистые поверхности.
детали со значительными
отклонениями формы в
поперечном сечении или
неравномерной твёрдостью
поверхности
ПРЕИМУЩЕСТВА МЕТОДА
1) сохраняется целость волокон металла и образуется мелкозернистая структура в поверхностном слое;
2) отсутствуют термические дефекты;
3) можно достигать минимального параметра шероховатости поверхности Rа = 0,1…0,05 мкм и даже менее.
4) можно образовывать регулярные микрорельефы с заданной площадью углублений для задержания смазочного материала;
5) создаются благоприятные сжимающие остаточные напряжения в поверхностном слое;
6) повышается микротвердость в поверхностном слое.
НЕДОСТАТКИ
а) значительная часть способов поверхностного пластического деформирования не повышает геометрической точности поверхности, обычно сохраняется точность, достигнутая на предшествующей операции;
б) при обработке тонкостенных деталей (толщиной от 3 до 5 мм) может происходить деформация поверхности в пределах от 5 до 10 мкм и даже более;
в) возможно образование наплывов металла толщиной от 0,03 до 0,3 мм.
ЗАКЛЮЧЕНИЕ
Поверхностное пластическое деформирование деталей применяется во всех типах производства.
Обработка поверхностным пластическим деформированием выполняется на многих металлорежущих станках, например, на токарных, строгальных или протяжных и может быть выполнена как самостоятельная технологическая операция или как один из переходов операции.
Обработка методом поверхностного пластического деформирования деталей машин может быть применена для любых металлов и сплавов, способных пластически деформироваться .
В ходе пластического деформирования шероховатость уменьшается на 30 %
ЛИТЕРАТУРА
1. С.Н.Колесов ,И.С. Колесов «Материаловедение и технология конструкционных материалов» учебник-М, «Высшая школа» 2004г, 250с
2.А.А. Черепахин. Технология обработки материалов. Академия. М. 2004г, 335с
3.«Материаловедение. Технология конструкционных материалов» Учебное пособие Под редакцией В.С. Чередмичеснко-5-е изд, М:-из-во «ОМЕГА-Л» 2009г
4 М.Е. Дриц, М.А. Мосалев «Технология конструкционных материалов и материаловедение»
М, «Высшая школа» 2001 г, 447с